Ever wondered how a well-organized warehouse can be a game-changer for your business? It’s all about maximizing space and efficiency. Effective warehouse storage plays a crucial role in the efficiency of the entire supply chain, impacting everything from inventory management to delivery speeds.
A cluttered warehouse can lead to delays and errors, frustrating customers and harming your bottom line. By understanding key storage strategies, you can ensure smooth operations and improve customer satisfaction. Whether you’re dealing with pallets, racks, or bins, the right approach can boost productivity and save costs.
What to Understand About Warehouse Storage
When you walk into a warehouse (see more here), it may seem like a vast sea of products, but there’s a method to the madness. Different storage systems keep everything organized and accessible, just like how a library has shelves for different book genres. Let’s explore the different types of warehouse storage solutions to see how they help businesses function smoothly.
Static Storage Systems
Static storage systems are like the sturdy bookshelves in a library. They stay in one place and hold items securely, making them perfect for products that do not need frequent movement. These systems are the backbone of many warehouses because they’re reliable and straightforward.
- Pallet racking: This is one of the most common types of static storage. Think of it as high-rise apartment buildings for pallets. They use vertical space efficiently, letting you stack goods safely without taking up too much floor area.
- Shelving: Similar to what you’d find at home but a bit more industrial. Shelves are great for smaller items and picking by hand. They come in various materials like metal or wood and can be adjusted to fit different product sizes.
Dynamic Storage Systems
Unlike static systems, dynamic storage solutions are on the move. Imagine a busy sushi conveyor belt, where dishes slide along to you. These systems work similarly, moving goods through the warehouse for better accessibility and speed.
- Mobile shelving: This type of shelving is on wheels, allowing you to move rows together and apart as needed. It maximizes storage in smaller spaces by eliminating unnecessary aisles.
- Flow racks: These racks use gravity to move inventory from the back to the front. When you remove an item, the next one rolls right up to take its place. It’s like the self-replenishing snack bar of storage systems, perfect for managing stock and keeping products fresh.
Automated Storage and Retrieval Systems (ASRS)
Technology takes center stage with ASRS (https://www.qmhinc.com/automated-storage-and-retrieval-system/), automating how items are stored and retrieved. This system reduces the need for human labor, increasing efficiency and accuracy.
- Technology behind ASRS: These systems use advanced computer-controlled equipment, including robotic shuttles, lifts, and conveyors. They handle the retrieval and placement of items with precision.
- Advantages: ASRS improves productivity by reducing time spent searching for products. It lowers the risk of errors and can operate 24/7, making it ideal for high-demand operations.
- Optimizing operations: By shortening retrieval times and optimizing space, ASRS can transform a warehouse into a lean, efficient machine. It’s more than just storage; it’s about rethinking how a warehouse works.
Space Utilization: Making Every Square Foot Count
Warehouse space is a valuable commodity. Poor layout or inefficient use can lead to wasted time and increased costs. Here’s what you can do:
- Vertical Storage: Take advantage of all available space. Stack goods vertically whenever possible to maximize storage capacity.
- Aisle Configuration: Keep aisles wide enough for equipment but narrow enough to save space. This balance reduces time spent maneuvering around the warehouse.
- Flexible Racking Systems: Use adjustable racking systems to accommodate various products and sizes. Being flexible with space allows for better adaptability to changing inventory needs.
Every piece has a perfect spot, and proper configuration leads to higher scores and efficiency.
Safety is Non-Negotiable
Safety isn’t just a priority; it’s a necessity. Keeping both staff and inventory safe protects your business from losses and liability.
- Regular Inspections: Routine checks help identify potential hazards before they become problems. Inspect racks and aisles frequently.
- Employee Training: Provide ongoing safety training. Ensure everyone knows how to handle equipment and materials safely.
- Proper Labeling: Clearly mark hazardous areas and materials. Labels guide staff, preventing accidents and confusion.
There’s no reset button on safety lapses, so being proactive is key.
Inventory Management: The Backbone of Efficiency
An effective inventory management system is the backbone of any warehouse storage operation. Staying organized can save time and money, turning chaos into order.
- Real-Time Tracking: Use technology to track inventory levels in real-time. Barcodes and RFID systems can automate updates and reduce human error.
- Cycle Counts: Conduct regular cycle counts instead of annual inventory checks. Smaller, frequent counts help maintain accuracy without significant downtime.
- Demand Forecasting: Use historical data and trends to predict demand. Knowing what’s needed in advance helps manage stock levels and prevent overstocking or shortages.
Conclusion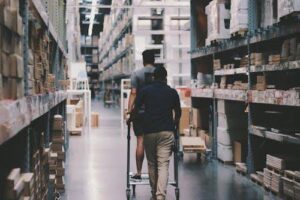
Warehouse storage isn’t simply about stacking goods. It’s about smart strategies that integrate space utilization, safety measures, and efficient management. Ensuring you have the right systems and processes in place can mean the difference between a chaotic warehouse and a symbiotic hub of productivity.